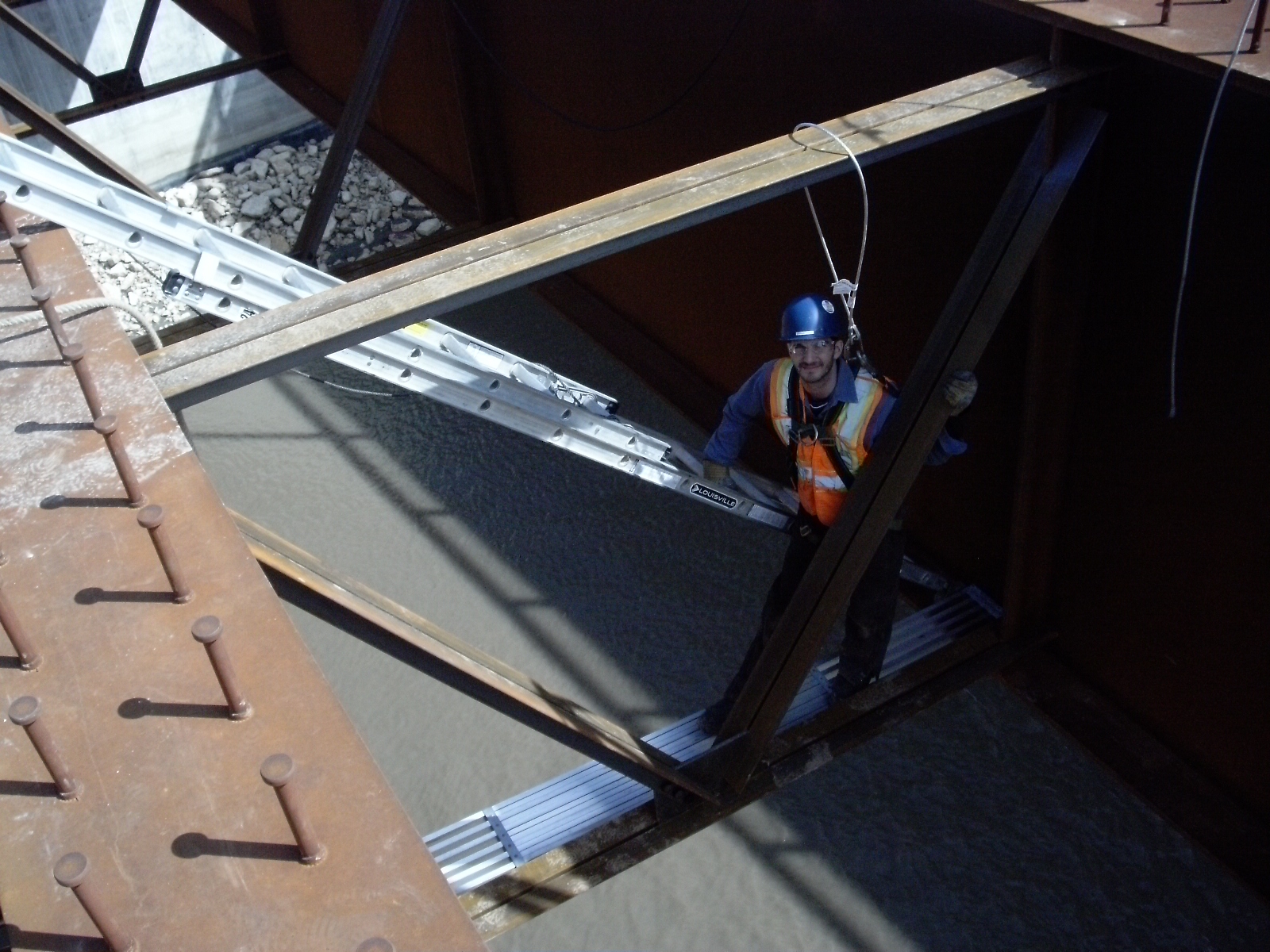
Implementing Safety
Every Industry is required by law to implement a safety program. However, this is a loose term, and it is often hard to know where to start.
When AXIS first began implementing a formal safety management system, we hired a coordinator and a consultant and paid a lot of money for a bunch of paper. After 18 months, we had a program that needed to be clarified, no formal certification or accomplishment, and most notably, no one had changed how they were working. A lot of money and time were spent on a “safety program” that didn’t make anyone safer than they were before.
At that point, I realized that, as the owner of a small business, it was up to me not to do all the work but to change my attitude about what safety meant. I truly wanted my employees to work safely and to go home each night, not only because if I didn’t, I might go to jail, but because I cared about them.
So what did I do? First, I realized that I can’t get it perfect. If it is perfect, there is no room for improvement. I genuinely believe that safety always has room for improvement. Next, I looked at the most hazardous aspects of our work. I looked through the safe work procedures provided by the consultant and discovered procedures for using a hammer and other “helpful” methods, but found nothing for our most hazardous tasks. I realized my frustration; this consultant gave us general safety information, but he didn’t take the time to understand what we really did.
After identifying our most hazardous activities, we started working on forms to assess these risks, developed inspection checklists for each, and worked through the training of these items with our employees. It was possible that during this time, they may hit their thumb with a hammer (unlikely because we don’t use them in our work), but I felt confident knowing that we were concentrating on the tasks that, if not done safely, would lead to severe injury or death.
Don’t get me wrong, there are too many incidents, but I knew there was no way to do everything simultaneously as a small business. A prioritized list with manageable tasks implemented was much better than a bunch of information that was never adopted.
Over the next month, I’ll be sharing some of the tools and resources we’ve developed over the past five years. I’m sharing these not because I want to claim ownership over safety, but because I believe that safety is a collective responsibility. If we’re working together on a job site, it’s in all of our best interests to have the best safety information available and to share our resources. Let’s work together to make our workplaces safer.
I would love to hear about any safety successes you have had!
Until Next week,
Bonnie Pankratz